

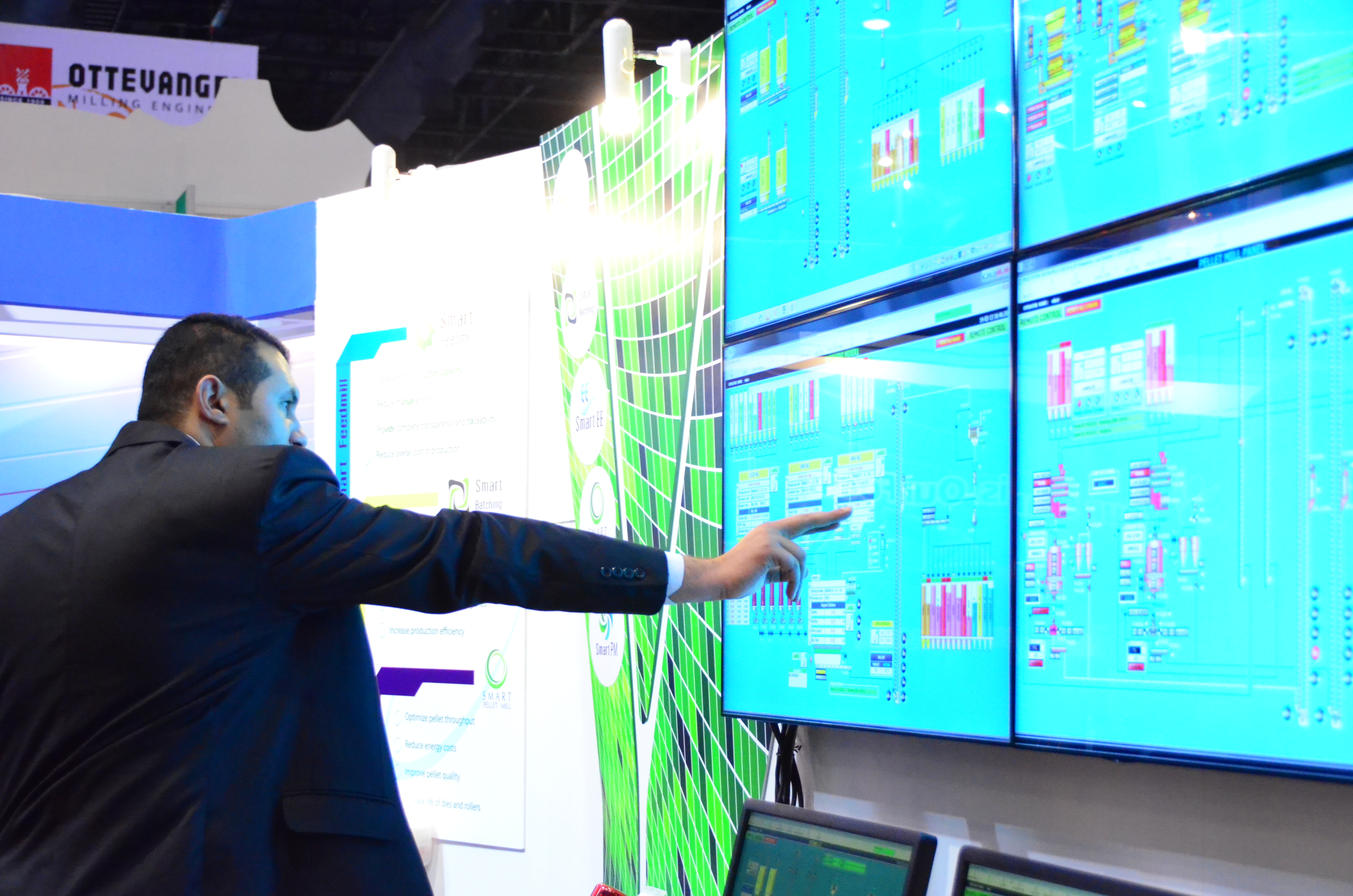

Description
Mill Plus is the most advanced and complete feed mill and premix automation system serving the Asian market. It is designed to be simple to operate but provide sophisticated levels of automation throughout every stage of the production process from gate to gate.
One of the major benefits of the MILL+ software is the ability for the data that is generated to be seemingly integrated with the clients own Management Information Systems. This provides a valuable tool for analysis of a wide range of data both in terms of operational and cost efficiencies as well as full traceability and stock reconciliation.
Benefits
- Optimizations of Feed Mill Production Capacity
- Provide all Reports Necessary to Manage a Feed Mill
- Reduce Human Reliance and Errors
- Minimize Stock Discrepancies
- Provide for Full Traceability and Feed/Food Safety
- Maximize Profits
Features
- Multi batching capability
- Can be integrated and contol any machinery and equipment
- Comprehensive and versatile reporting system
- Complete feed mill process automation and truck management system
- Provides multiple management reports
- Robust Traceability and Cross contamination control
- Can be implemented in any existing mills or new builds
- Data can be easily integrated with management information systems
Suite Application
Modules
Suites







Description
A complete process control and data reporting system covering raw material receiving, grinding, batching, weighing, mixing, micro dosing, conditioning/pelleting, cooling, fat coating and finished product loading and packing. Designed to provide full traceability and mill capacity optimization.
Smart Feedmill can also seemingly integrated with the clients own Management Information Systems to help provids a valuable tool for analysis of a wide range of data both in terms of operational and cost efficiencies as well as full traceability and stock reconciliation.
Benefits
- Optimization of Feed Mill Production Capacity
- Provides Reports Necessary to Manage a Feed Mill Efficiently
- Optimize Manpower Resources and Reduce Human Errors
- Minimize Stock Discrepancies
- Meets International standards for Traceability and Food Safety
- Maximize Profits
Features
- Can be implemented in any existing mills or new builds
- Can be integrated and control any machinery and equipment
- Comprehensive and versatile reporting system
- Data can be easily integrated with management information systems
- Robust Traceability and Cross contamination control
- Multi batching capability
- Can be implemented as a scalable modular system
Suite Application
Modules
Suites




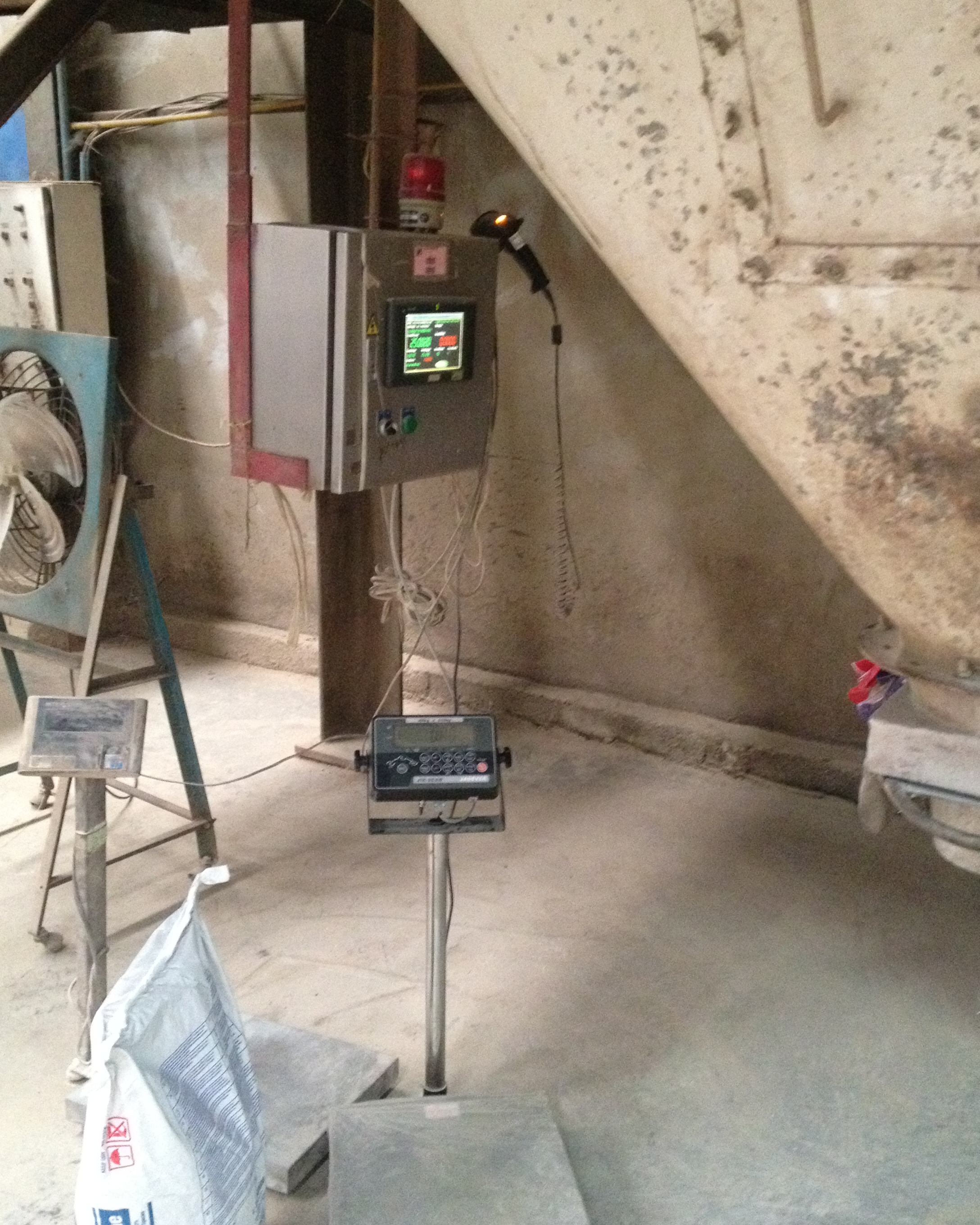
Description
A complete process control and data reporting system specifically for premix production plants covering receiving of ingredients, batching and weighing, mixing and finished product packing and loading. Designed to provide full traceability and compliance with international standards of food safety.
Benefits
- Eliminating concerns about cross contamination
- Accuracy of addition and dosing of ingredients and additives
- Reduce weighing and hand addition errors; human errors and product wastage
- Precision and consistency of premix specifications
- Compliance with legal declarations and International Assurance schemes
- Customer Satisfaction
- Real time stock reconciliation and traceability
- Minimizing the influence of the human factor
Features
- Automated Cross contamination prevention and flush batch control
- Bar Code technology and Touchscreen displays
- Continuous recording of lot numbers and individual weights
- Can be integrated and control any machinery and equipment
- Comprehensive and versatile reporting system
- Provides multiple management reports
- Multi batching capability
- Precision Dosing and weighing
- Computerised formulation and tolerance control
- First In First Out Tracking and Tracing
- Data can be easily integrated with management information systems
Suite Application
Modules
Suites



Description
A newly launched module that is designed to provide a solution for the accurate control and tracking of raw materials from intake receiving to storage silos or warehouses and from the storage areas to production.
Benefits
- Accurate control and documentation of all incoming bulk ingredients
- Preventing silo filling errors and cross contamination
- Optimization of raw material product silos and storage management
- Real-time stock reconciliation and traceability
Features
- Automatic direction control of incoming ingredients to and from bulk storage facilities
- Correct selection of silos and warehouses for bulk ingredients
- Can be integrated with other data monitoring systems to route ingredients based on defined parameters, e.g. moisture
- Comprehensive reporting system on all incoming ingredients
Module Application
Modules
Suites




Description
The control of the weighing and mixing systems is at the heart of the production process. Smart Batching is a high precision weighing and mixing process control program resulting in formulation accuracy and consistency.
Benefits
- Optimize production planning
- Eliminates weighing errors and human errors
- Reduced batching time
- Precision and consistent feed specifications
- Prevent cross contamination
Features
- Automatic Import of formulations
- Comprehensive and versatile batching reporting system
- Automated Cross contamination prevention and flush batch control
- Digital discharge control of bulk raw ingredients, liquids and hand additives
- Intelligent free fall weight calculation, automatic jogging, multiple feeders, pre-discharging and intelligent feeder control
Module Application
Modules
Suites



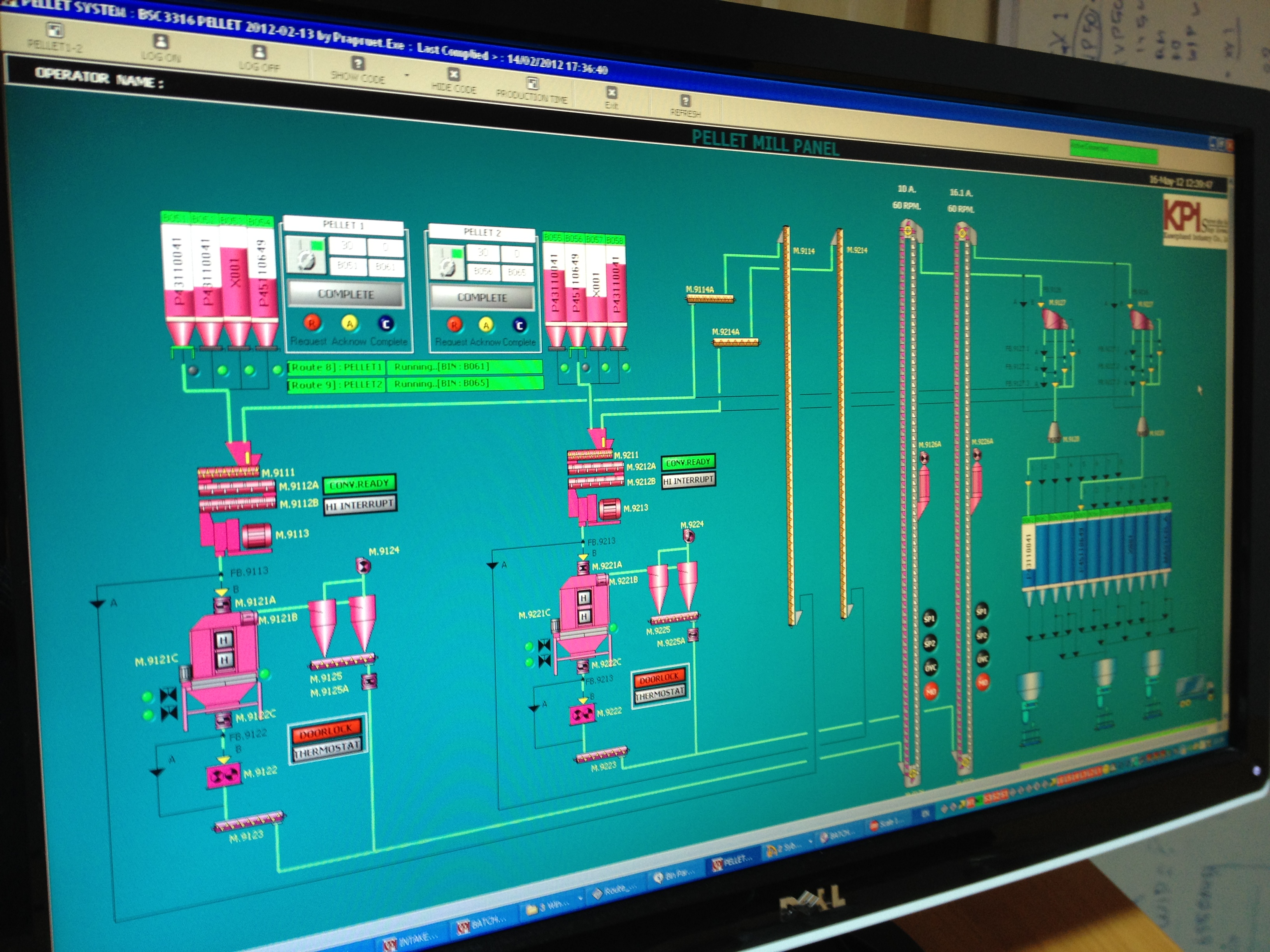
Description
Smart Pellet is designed to optimize pellet mill throughput, improve pellet quality and reduce blockages and down time. All configurations of expanders, conditioners, fat spray at the die and pellet mills can be handled. User friendly interface with touch panel is used as the communicating unit.
Benefits
- Increase production throughput
- Reduce energy costs
- Improved pellet physical quality and consistency
- Extended life of pellet mill dies and rollers
Features
- Full Automatic start up
- Continuous Blockage and choke point detection
- Capacity to preload and store multiple formulations and their specific parameters
- Continuous change over function which allows a press bin to start the next product without delay
- Pre-set production parameters for every formulation, including steam settings, temperature and throughput
Module Application
Modules
Suites

Description
Smart Premix is designed to remove the risks and errors associated with the manual preparation and weighing of premix ingredients, additives and medicines.
Benefits
- Eliminating concerns about cross contamination
- Accuracy of addition of ingredients and additives
- Reduce potential addition errors; human error, wastage of ingredients
- Precision and consistency of premix and feed formulated specifications
- Real time stock reconciliation and traceability
Features
- Bar Code technology and Touchscreen displays
- Stand-alone system compatible with single or multiple preparation stations
- Integrated control with formulation and batching system
- Continuous recording of lot numbers and individual weights
Module Application
Modules
Suites

Description
Hand Add is designed to remove the risks and errors associated with the manual addition of hand additives to the mixer. Combining barcode and LCD technology, only the correct type and quantity of premix, ingredients and additives can be discharged into the mixer.
Benefits
- Eliminating concerns about cross contamination
- Accuracy of addition of ingredients and additives
- Reduce potential addition errors; human error, wastage of ingredients
- Precision and consistency of premix and feed formulated specifications
- Real time stock reconciliation and traceability
Features
- Stand-alone system compatible with single or multiple hand dump stations
- Bar Code technology and Touchscreen displays
- Integrated control with formulation and batching system
- Continuous recording of lot numbers and individual weights
- Hand addition identification and timing to mixer control
Module Application
Modules
Suites





Description
Process control of single or multiple intake points to ensure that only the correct raw materials can be tipped at the designated intake and directed to the appropriate silo. This module provides real time stock movement and inventory information and removes the risk of tipping errors.
Benefits
- Preventing silo filling errors and cross contamination
- Accurate control of incoming bulk ingredients
- Accurate and real time stock inventory
- Optimize the utilisation of raw material product silos
- Ensure continuous supply of raw material to meet production requirements
Features
- Real-time stock reconciliation and traceability
- Can be directly linked to the weightbridge
- Works in parallel withe Route Control and in flight weighting systems
- Tipping procedure can be initiated by Bar Code
- Conveyor Start/stop / hold commands
- Message and information display system at each Intake Station
Module Application
Modules
Suites


Description
A highly advanced automated system that links the different modules and can control and track the movement of any ingredient or feed at any point within the feed production process. Not only does this prevent routing errors it provides the necessary traceability compliance required within the EU and other major food importing regions.
Benefits
- Eliminating concerns about cross contamination
- Enables same time multi batch production
- Improves plant capacity/li>
- Data generated can be used to monitor and review operators performance
Features
- Auto route selection
- Start and stop equipment along the route selected
- Compatibility matrix for prevention of cross contamination
- Simultaneous Multi batching capability
- Report generation and traceability
- Real time display of material movements
Module Application
Modules
Suites

Description
Smart Bagging module is a comprehensive process and data management system for bagging stations that collects and displays information relating to packing line key performance indicators, product details and operators efficiency.
Benefits
- Improved operator and packing line efficiency
- Provides for accurate stock management
- Precise control of individual bag weight
- Prevents bagging errors
- Reduced manual interface
Features
- Packing bin discharge control
- Records number, size and weight of bags or pallets individually and collectively
- Stock reconciliation based upon actual number of bags produced per batch
- Monitor next to each packing station displaying real time bagging line data
- Pallet tag function with option to communicate with inkjet bag labeling systems
- Report generation with option to export to Management Information Systems
Module Application
Modules
Suites


Description
A highly advanced automated system that links the different modules and can control and track the movement of any ingredient or feed at any point within the feed production process. Not only does this prevent routing errors it provides the necessary traceability compliance required within the EU and other major food importing regions.
Benefits
- Eliminating concerns about cross contamination
- Enables same time multi batch production
- Improves plant capacity/li>
- Data generated can be used to monitor and review operators performance
Features
- Auto route selection
- Start and stop equipment along the route selected
- Compatibility matrix for prevention of cross contamination
- Simultaneous Multi batching capability
- Report generation and traceability
- Real time display of material movements
Module Application
Modules
Suites




Description
A system specifically developed for the accurate individual counting of bags or goods as they pass along a conveyer. Simultaneously Smart Belt ensures accurate inventory and efficient and timely loading or unloading of products.
Benefits
- Prevent and record loading errors or fraudulent activities
- Precise control and documentation of all incoming or outgoing products
- Provides for accurate raw materials or finished goods stock management
- Data generated can be used to monitor and review operators performance
Features
- Alarm function
- Create job reports
- Display real time performance against job defined targets
- Create loading or unloading job plan with operator targets
- Smart Belt technology in combination with Optical sensors that measures the length of each bag to prevent errors or fraudulent activity
Module Application
Modules
Suites



Description
A unique product developed specifically for the often complex and labor intensive process of monitoring and controlling trucks once they arrive or depart from the feed mill. Truck Plus incorporates Quality Control, Administration, Procurement, Stock Control and Traffic Control procedures.
Benefits
- Increased transport turn-around time
- Provides security and transparency
- High level traceability
- Reduced manual entry, labour cost and paperwork
- Ensures accuracy of loaded or unloaded weights
- Maintains real time inventory
Features
- Provides for accurate loading of finished feeds or unloading of raw materials
- Bar code technology ensures the trucks follow the correct assigned destination while in the facility
- Provides a common platform for both incoming and outgoing trucks to be registered, processed and appropriate actions assigned
- Information is instantly transmitted to multiple stations via internal communication network
- At the work station information is reviewed, captured and used for further decision making processes
- The movement of each truck is controlled and timed to and from each station as directed
Module Application
Modules
Suites



Description
Winner of the 2012 GRAPAS Innovation Award for Milling LOGO
Winner of the 2012 GRAPAS Innovation Award, Queue Plus is a state of the art truck queuing system. The platform provides the facility to plan, monitor and control the movement of trucks and their personnel while on site. This is achieved by displaying live status feeds on digital screens, calling announcements and entry, destination and exit checkpoints.
Benefits
- Avoids uncontrolled trucks and personnel movement on site
- Demonstrates and maintains organization and discipline
- Improved customer experience
- Reduces product loading and unloading times
- Optimizes production planning and inventory turnover
Features
- Advanced or on the day queue booking and planning
- Data capture of truck information, times and loading details
- Queuing is communicated by voice announcement system and digital displays
- Digital screens display information regarding truck status, truck registration number, estimated waiting time and the assigned destination bay when called.
- Queuing can be scheduled according to client status, product availability, loading bay availability and time
Module Application